Sheraton Sewer Repair in San Diego: How to Completely Renovate the Entire Hotel’s Sewer System in 45 Days
Major repairs of sewer systems in large buildings are tasks that require a highly qualified approach and the use of modern technologies. In this case study, we describe how the specialists at Almco Plumbing carried out repairs on the sewer lines at the Sheraton Hotel, which ran at various depths. Modern cleaning methods and trenchless repair techniques were employed, enabling the business owners to save significant amounts of money and have the building operational within just a month and a half.
Read about the challenge to our professionalism below.
Contents
Technologies & Services
Client’s Problem: Key Objectives & Scope of Work
The Sheraton Hotel in San Diego, California, comprises five buildings of varying sizes and floor counts. The Almco Plumbing team was tasked with the following key objectives:
- Clearing pipelines of clogs, scale, and mineral deposits
- Completely replacing worn vertical sewer pipes installed within the walls
- Applying an epoxy coating inside all underground sewer pipes
- Verifying the airtightness and functionality of the upgraded system
A distinctive challenge of this project was the variable depth of the sewer system, ranging from 2 to 8 feet. Employing traditional trenching methods in this case would not only have extended the project duration significantly but also would have resulted in substantially higher costs.
Almco’s Solution: Step-by-Step Process Description
The repair work encompassed cleaning, restoration, and replacement of the sewer systems, as well as testing their functionality. The project was completed in 45 days—from November 1 through mid-December. Below is a detailed, step-by-step description of the entire repair process.
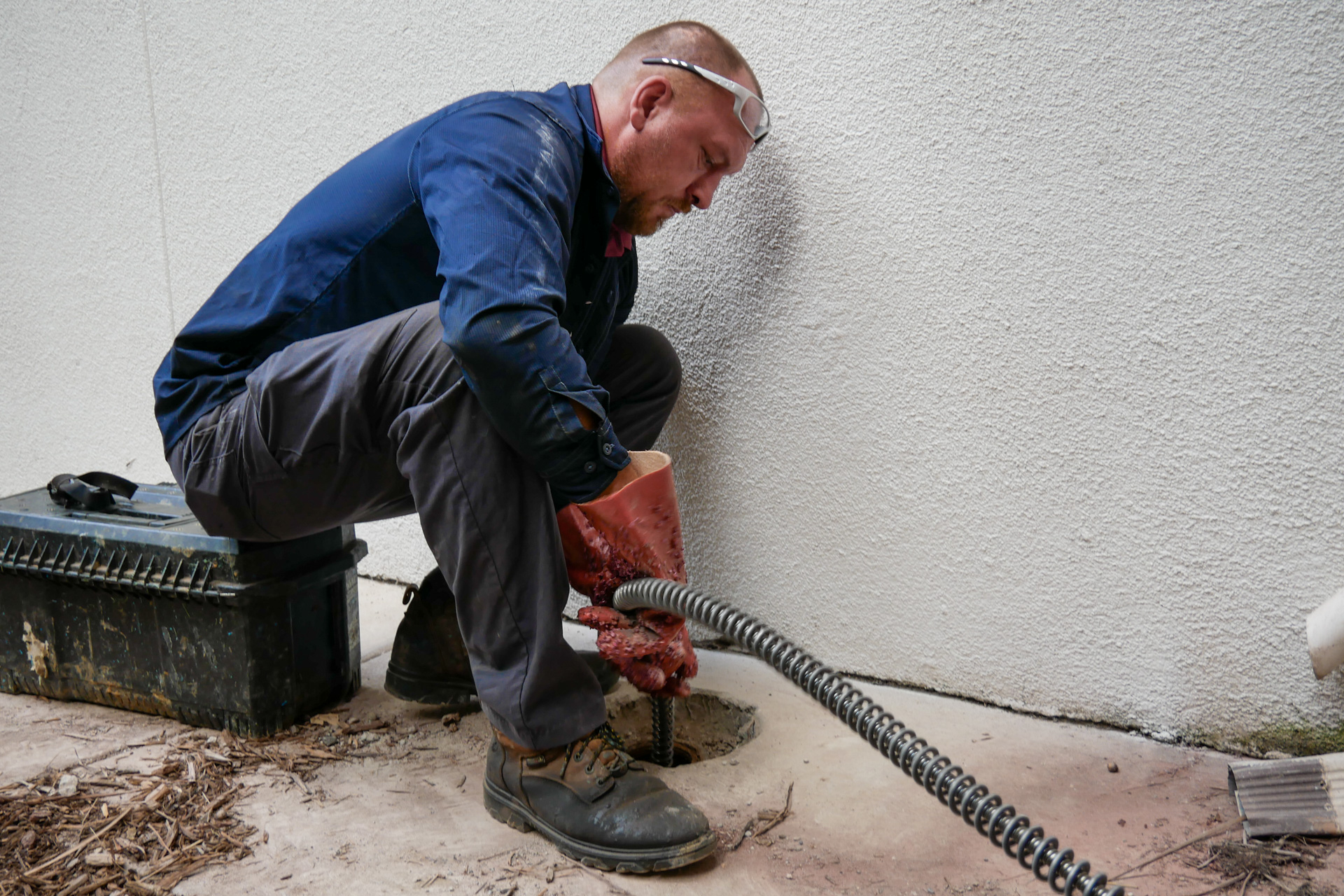
The main hotel pipelines, ranging from 2 to 8 inches in diameter, were heavily soiled. To eliminate clogs and buildup, a rotary shaft equipped with a mobile three-blade head was used. This head was manufactured from ultra-durable tool steel with a corundum coating on the cutting edges of the blades and earned the nickname “Electric Eel” for its efficiency in cleaning the problem areas.
After removing the deposits and obstructions, a powerful industrial vacuum was used to clear any remaining debris from the pipelines.
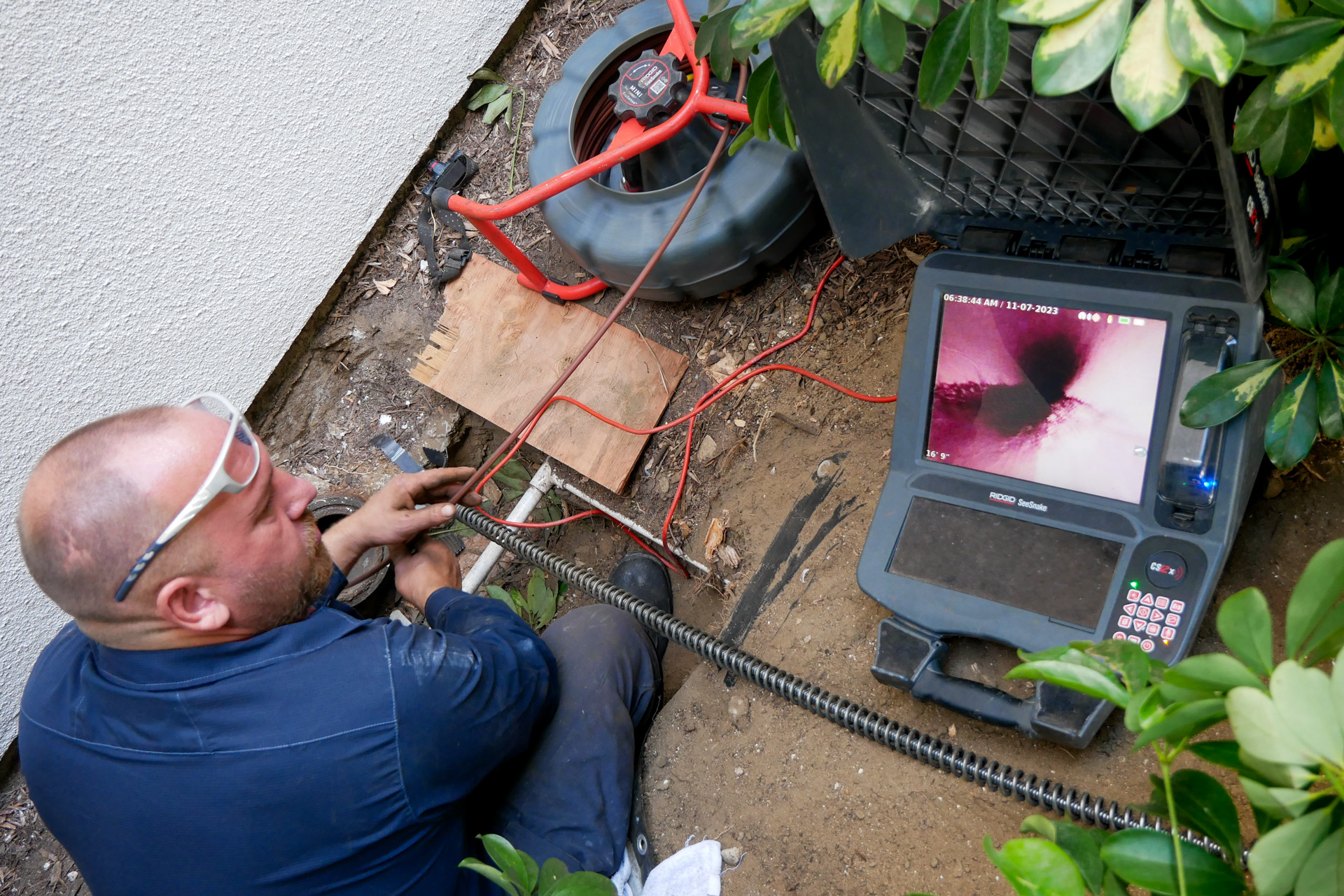
Once the initial cleaning was completed, a diagnostic inspection using video equipment was carried out.
This stage allowed the team to identify which sections of the pipeline required restoration and which needed to be completely replaced.
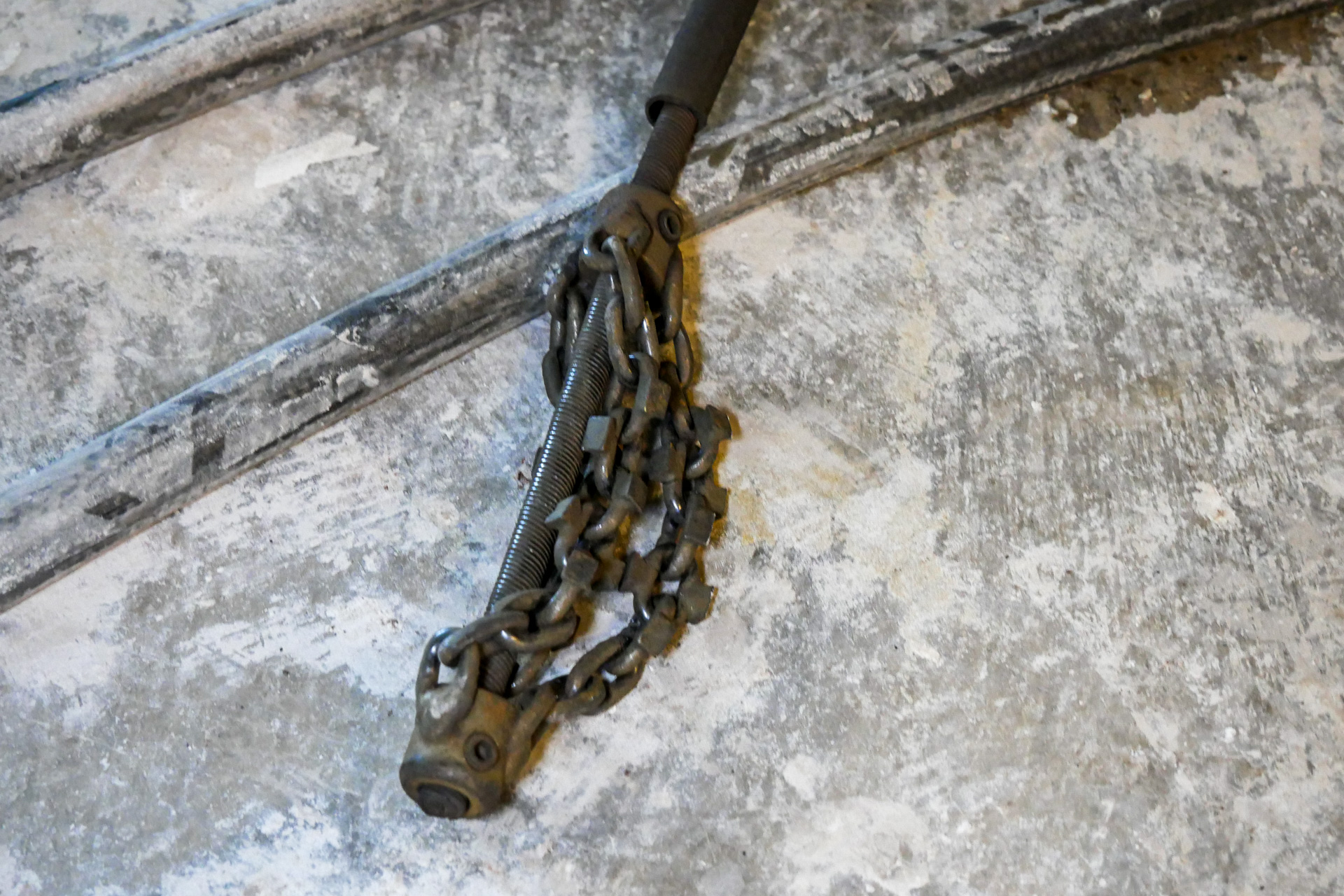
For the thorough cleaning of the pipes designated for restoration, a rotary drill fitted with ultra-durable carbide chains was employed. This process removed scale and corrosion, restoring the correct cross-sectional profile along the entire internal surface of the cast-iron pipes—preparing them for a high-quality bond with the epoxy coating.
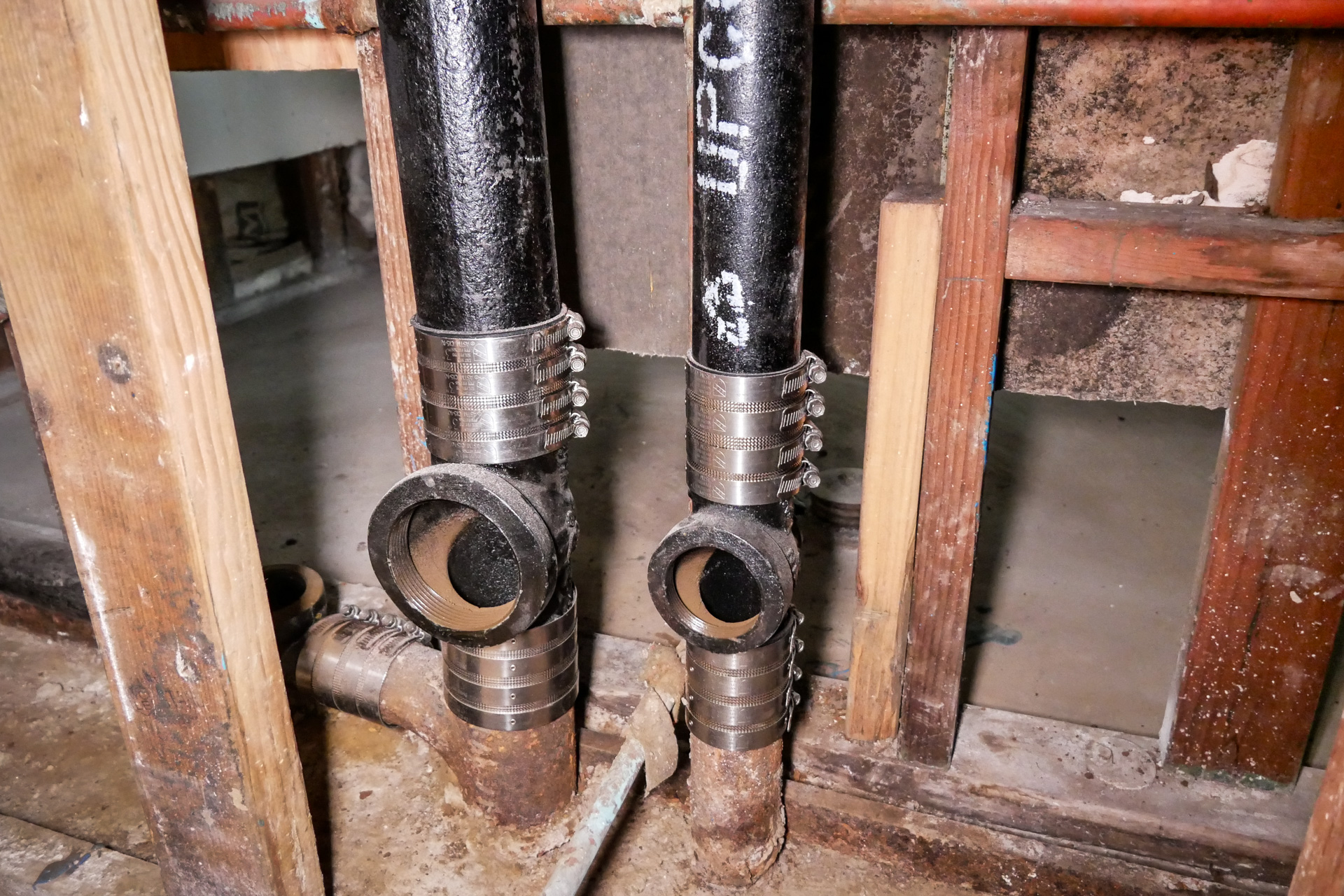
In 153 of the hotel’s rooms, the old cast-iron pipes and traps were replaced with new cast-iron ones.
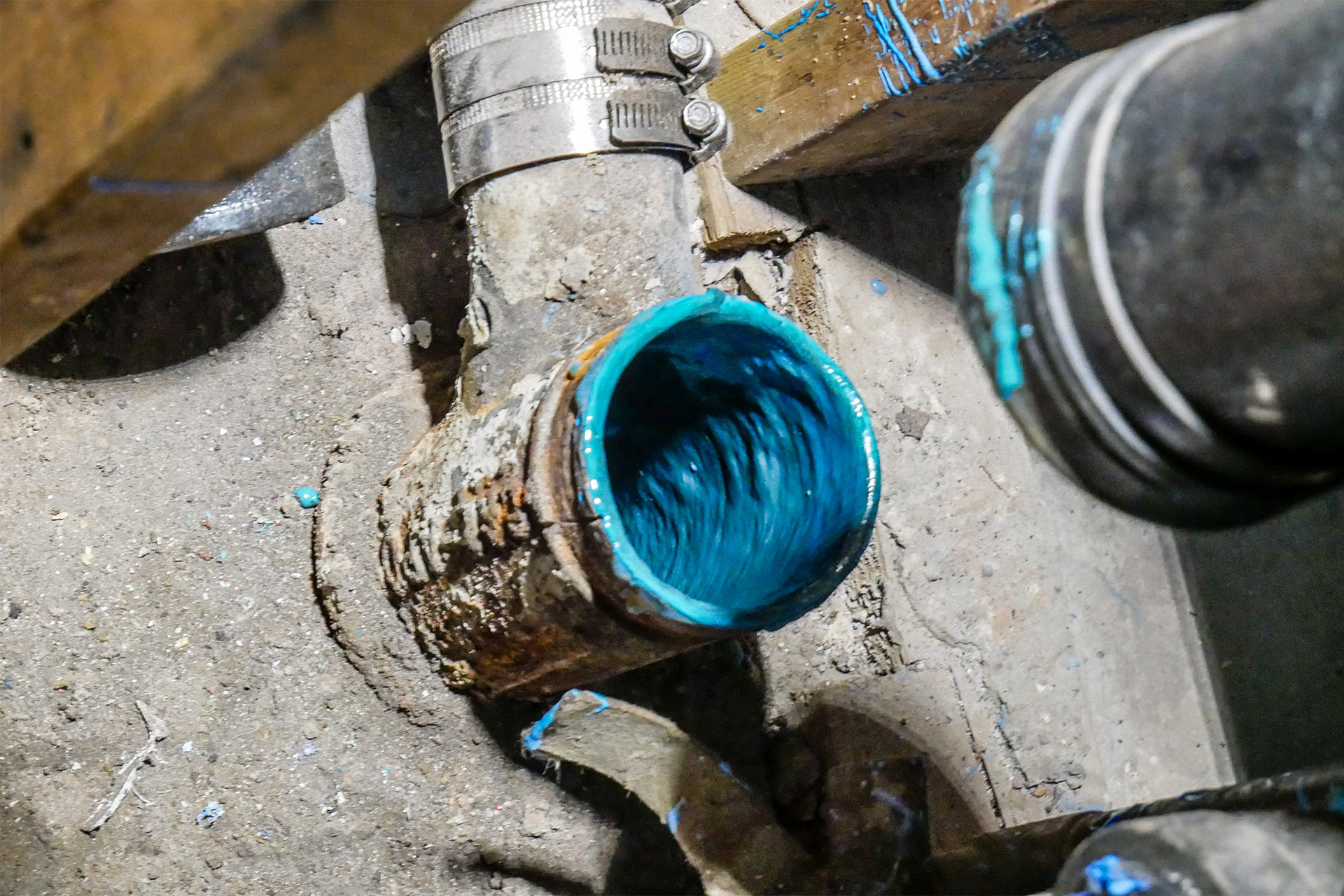
To restore the inner surfaces of the pipes, the epoxy lining technology was employed. Over 1,000 feet of pipeline were treated with epoxy resin, which not only remedied existing damage but also protected the pipes from further corrosion. Special attention was given to severely damaged sections, where an extra layer of coating was applied.
At every stage, an engineer from the company closely monitored the process using video diagnostic equipment, ensuring the even distribution of the epoxy compound. The bright pigment in the applied resin served as a clear indicator of the coating quality.
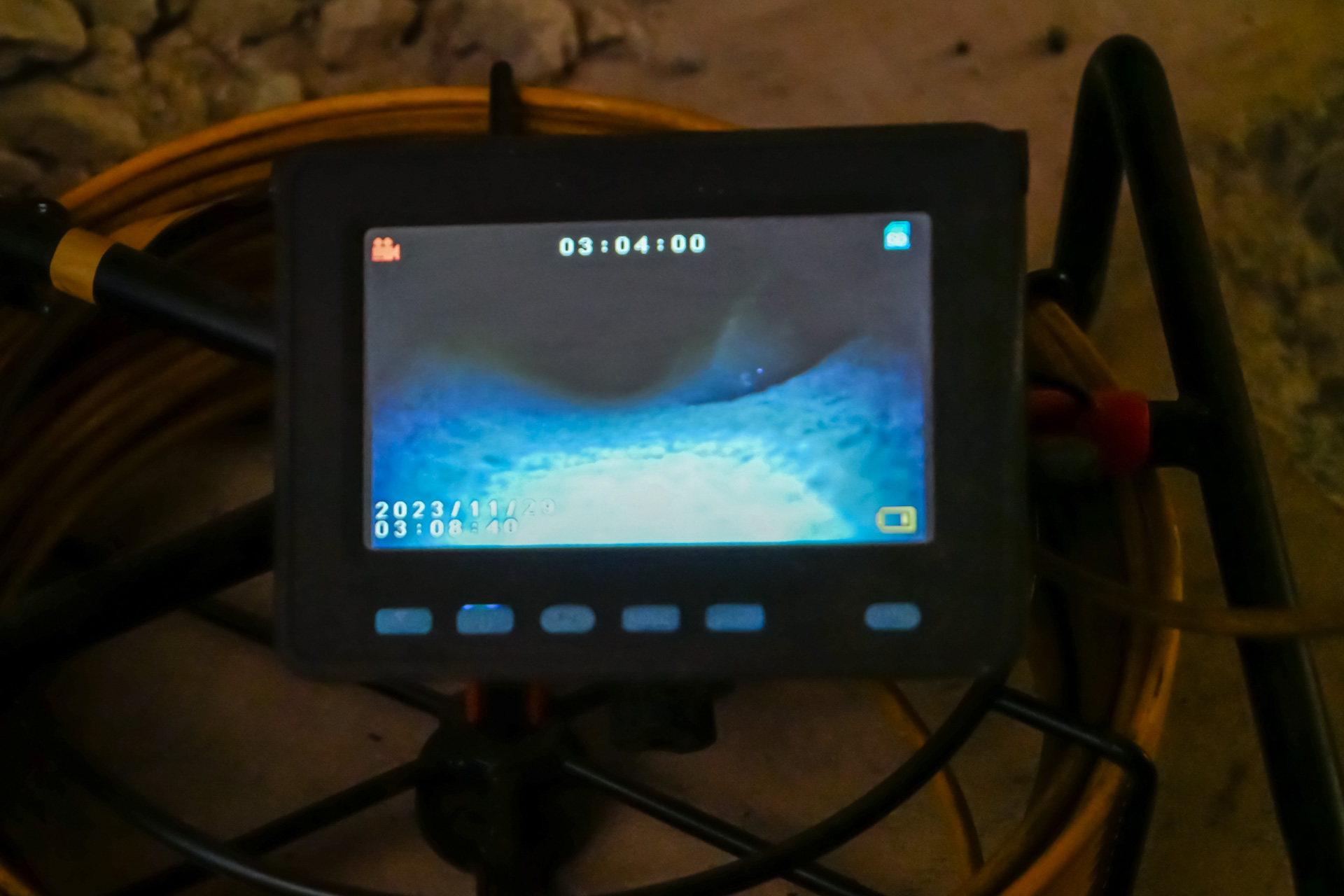
After the restoration compound fully cured—taking approximately 40 to 60 minutes—a follow-up inspection was conducted using video diagnostics to confirm the restored section’s functionality.
The final phase involved testing the system’s airtightness under various water pressure levels. Every section of the pipeline was tested to ensure complete functionality.
Advantages of Epoxy Pipe Lining in This Project
Utilizing epoxy lining technology allowed for a significant reduction in both the costs and time required for a complete overhaul of the sewer lines. This method is even suitable for pipes with severe damage, as the epoxy coating restores the structural integrity of the pipes and prevents further deterioration.
Economic Advantages for Business
The application of epoxy pipe lining considerably lowers the financial burden associated with major sewer system renovations since the restoration coating is applied inside the existing pipes. This approach is far more cost-effective than a complete replacement with new pipes.
Environmental Efficiency of the Technology
Epoxy lining technology offers significant environmental benefits:
- Waste Reduction: It minimizes the amount of waste generated from dismantling old pipes. Replacing entire pipelines produces a large volume of construction debris that must be disposed of, whereas restoring the existing system greatly reduces waste.
- Durability: The epoxy compounds used are highly resistant to chemical and biological influences, extending the service life of the pipes and reducing the need for frequent repairs or replacements. This, in turn, cuts down on the resources and energy required to produce and install new pipes.
- Minimal Disruption: Since the restoration work is performed without dismantling the pipes, the impact on the surrounding environment is minimized. This is especially crucial in densely built urban areas where pipe replacement could cause significant noise, dust, and disruption to the local ecosystem.
Results & Conclusions
In just 45 days, Almco Plumbing specialists completed a large-scale sewer infrastructure renovation across the five buildings of the Sheraton Hotel. They restored 26 vertical drain stacks, replaced the failing cast-iron pipes in 153 rooms with new ones, and refurbished over 1,000 feet of sewer lines.
Thanks to innovative methods and efficient project management, the upgraded sewer system now meets modern standards for reliability and durability.
Based on this experience, Almco Plumbing recommends the approach described above for other large-scale sewer modernization projects.