How CIPP Lining Reduces the Cost of Major Sewer Renovations in a Private Home: A Real-World Case from Almco Plumbing
Current maintenance, repair, replacement, and restoration of sewer and water supply systems are crucial aspects of managing a private home—especially in urban environments with increasingly demanding infrastructure standards. Over time, pipes deteriorate, leading to leaks, corrosion, and reduced capacity throughout the system. The following case study from Almco Plumbing demonstrates the advantages of CIPP (Cured-In-Place Pipe) lining technology by showcasing the restoration of a 3-inch cast iron sewer pipe without its complete replacement.
Contents
Technologies & Services
Client’s Problem & the Solution from the Almco Plumbing Team
The Almco Plumbing team responded to the client’s call to restore a cast iron, 3” pipe embedded in the foundation of a private residence. To minimize the costs associated with a full-scale overhaul of the sewage system, a thorough inspection of the sewer was conducted, leading to the decision to employ CIPP lining technology.
CIPP (Cured-In-Place Pipe) lining is an innovative method that enables the rehabilitation of a pipe without the need for complete replacement. This technique involves creating a new interior lining by applying an epoxy resin onto a felt base within the damaged pipe, thereby significantly reducing both the time and expenses typically associated with traditional repair methods.
Advantages of the CIPP Lining Method
- Cost-Effectiveness: CIPP lining offers substantial savings compared to conventional pipe replacement methods, which usually require extensive trenching to remove old pipes and install new ones.
- Speed: The entire repair process, including the installation of the liner, can be completed within a matter of hours.
- Durability: The newly formed liner has an impressive lifespan, often reaching 50 years or more, thanks to its excellent resistance to both mechanical stresses and chemical exposure.
- Environmental Friendliness: This method minimizes environmental impact by eliminating the need for large-scale excavation and reducing the volume of construction debris.
Step-by-Step Repair Process Using CIPP Technology
Below are the key stages involved in restoring worn, corroded pipes.
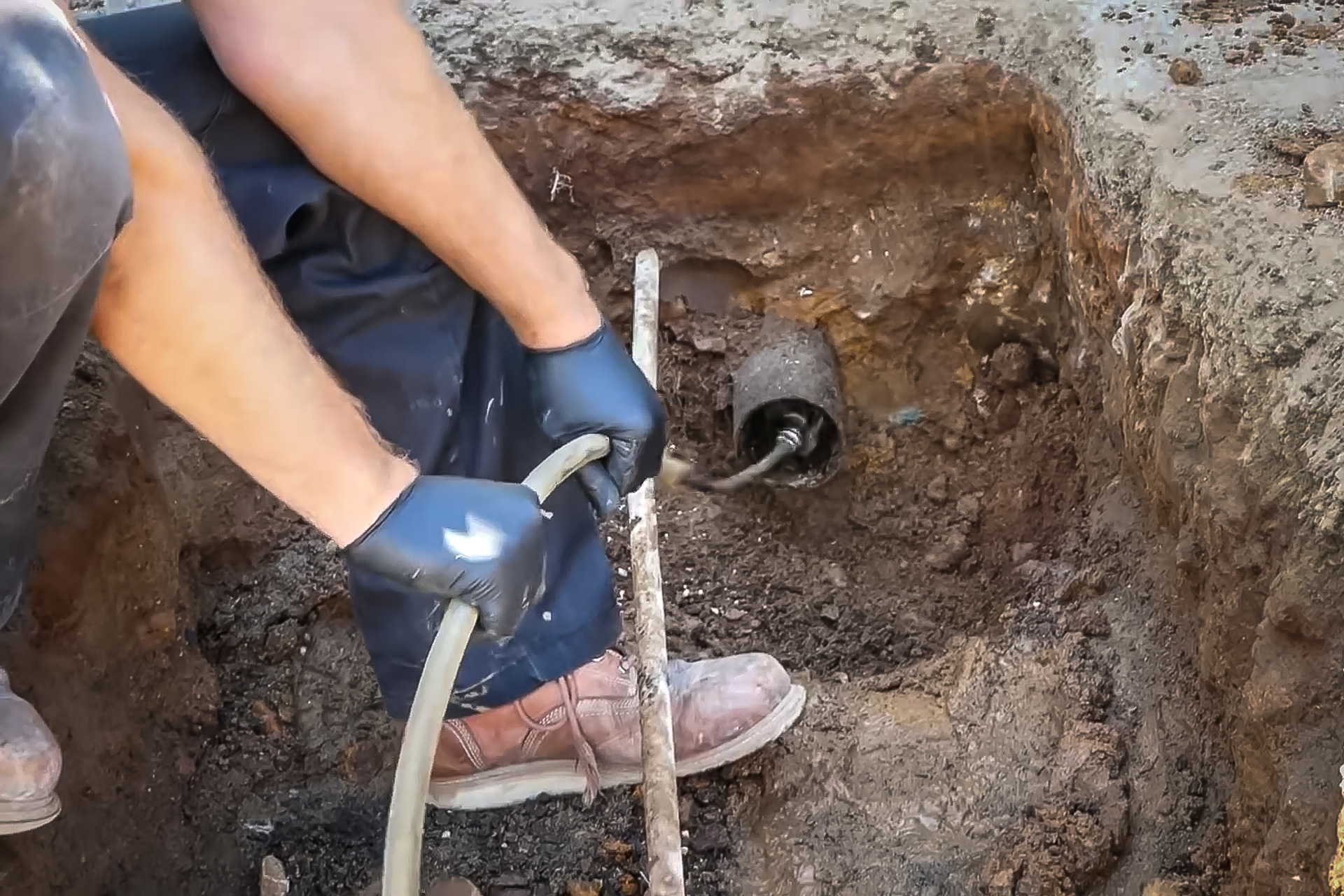
The quality of the epoxy resin’s adhesion directly depends on how thoroughly the inner surface of the pipe is prepared. This stage consists of two main steps:
- Mechanical Cleaning: Specialists from Almco Plumbing employ specially designed high-strength carbide chains to remove mineral deposits and other hard contaminants.
- Hydro-Jetting: A controlled, high-pressure water stream removes any remaining residues, fine particles, and dust.
This combined treatment creates the ideal conditions for installing the liner, ensuring excellent adhesion between the resin-soaked liner and the inner surface of the pipe.
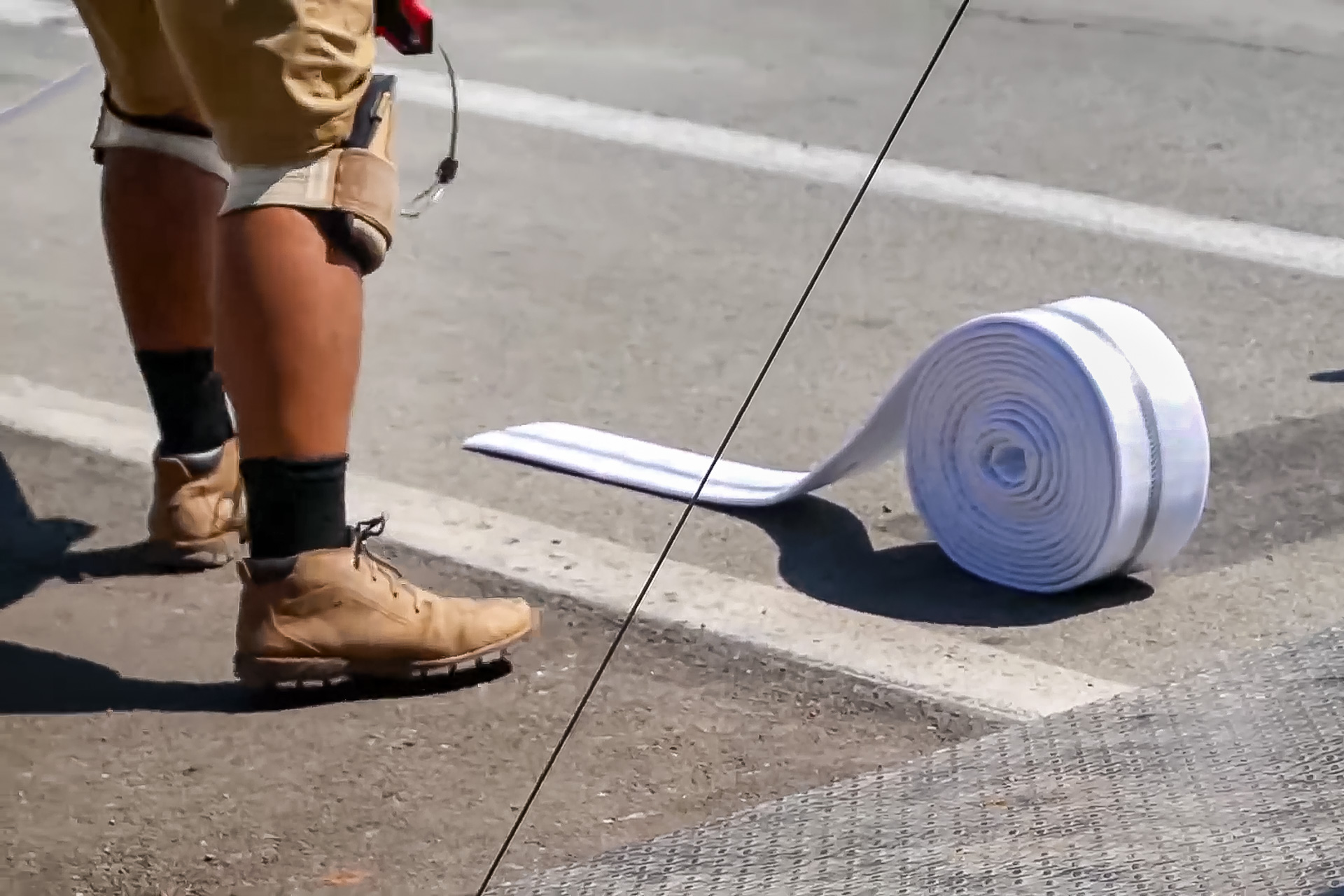
The size of the felt liner is selected according to the inner diameter of the pipe undergoing repair. It must be free of twists, folds, or compressions that could obstruct the free flow of liquids once the resin hardens.
The length of the pipe is measured, and a special felt sleeve is prepared to the required specifications. This sleeve serves both as the base for the epoxy resin and as a reinforcing material, with its fibers being saturated by the resin.
The required quantity of resin is measured by weight (using a formula to calculate the resin and hardener proportions), then thoroughly mixed and poured into the prepared sleeve. This “wetting” process saturates the liner with resin, readying it for installation.
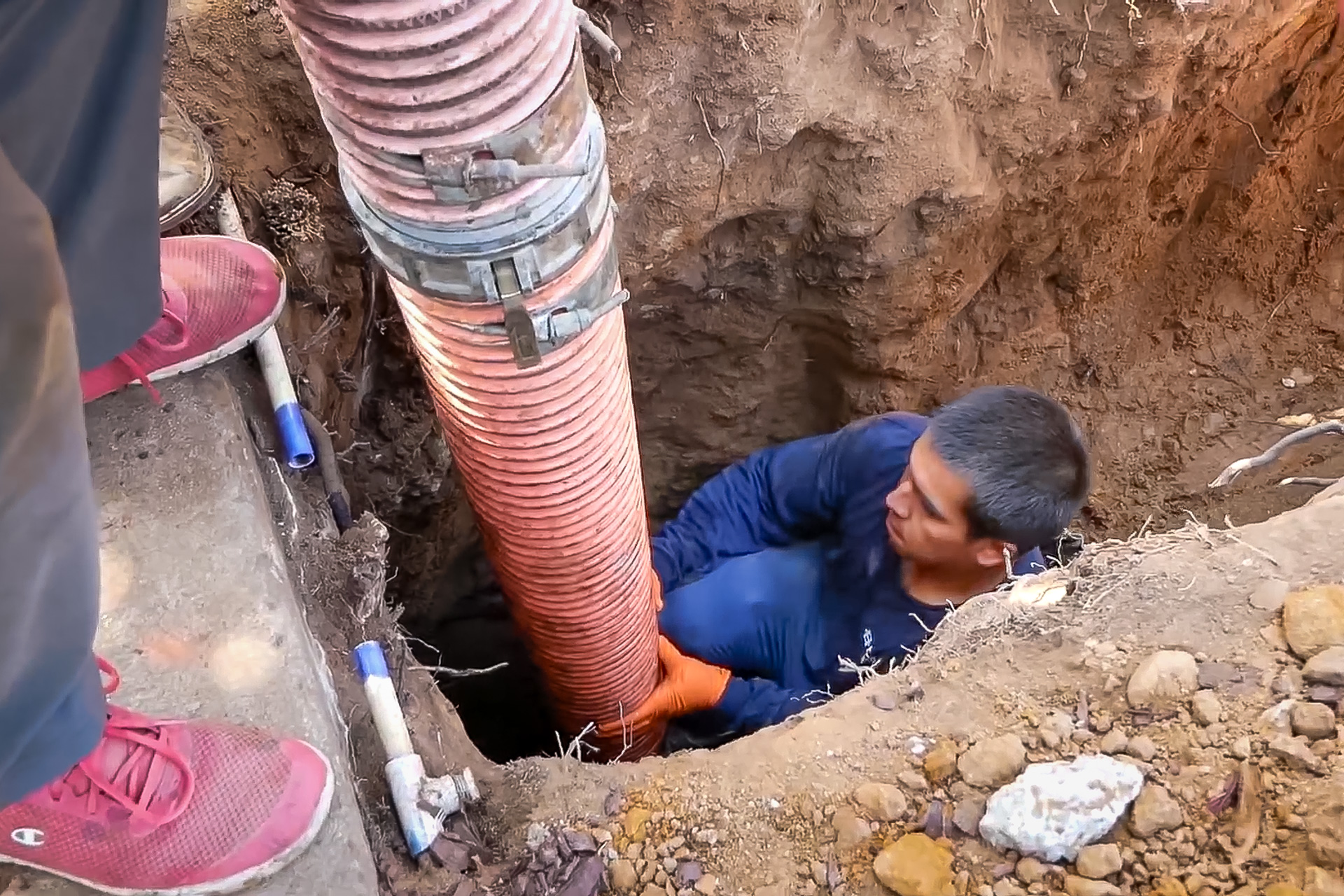
The resin-impregnated liner is loaded into the installation unit, which is connected to the repair pipe’s opening by a technological sleeve. Inside the pipe, the prepared felt liner is inverted (“turned inside out”) by high-pressure air introduced into the installation unit via a special nozzle. This inversion ensures that the epoxy resin, applied to the felt base, adheres tightly to the inner wall of the pipe.
Following the inversion, the liner is further inflated using an air bladder, into which compressed air is pumped. The resin-saturated felt fibers bond firmly with the pre-treated internal surface of the pipe. The resin typically takes about three hours to cure, after which the air bladder is removed, leaving behind a robust, high-performance epoxy coating inside the pipe.
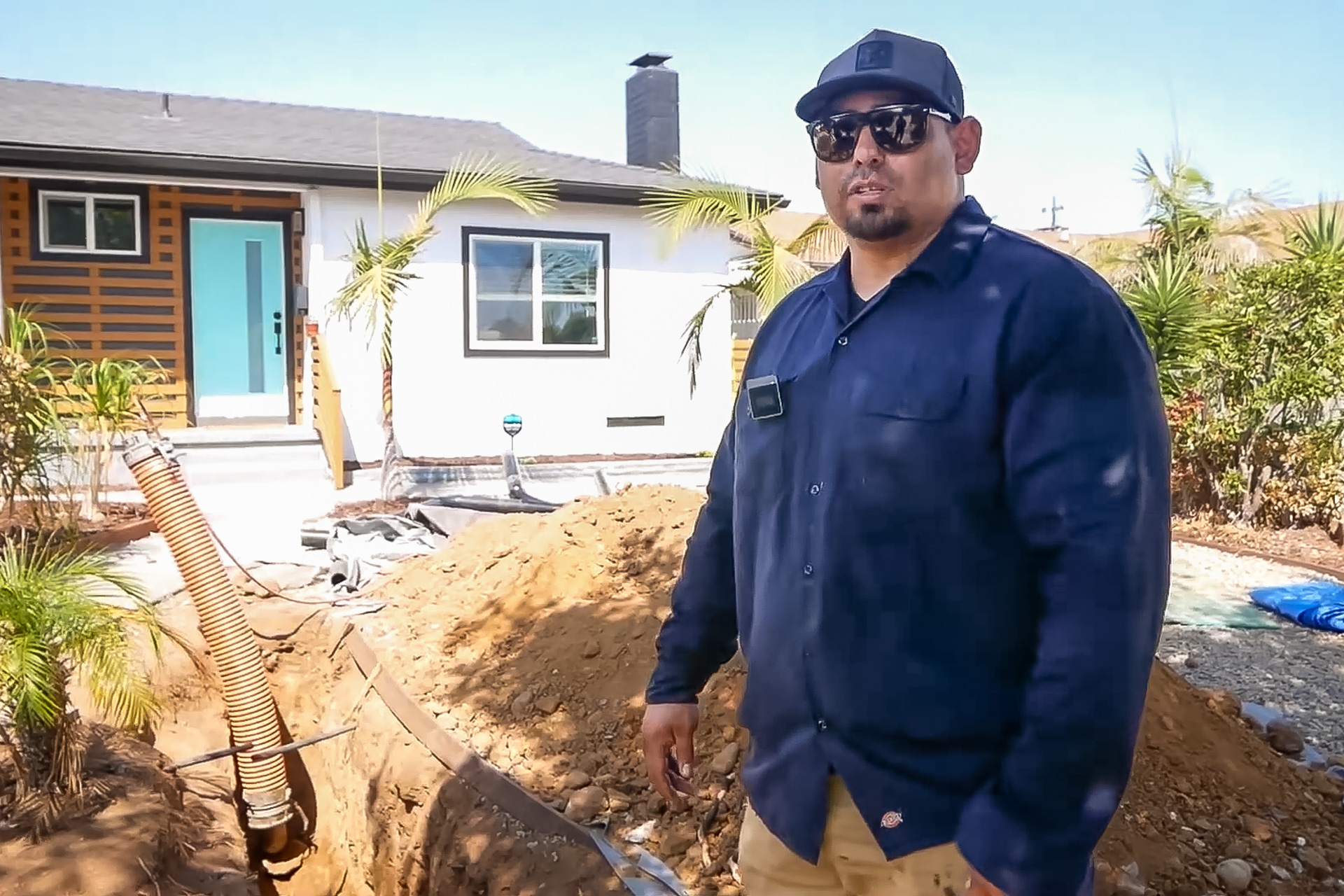
The final stage involves verifying the quality of the repair work. Video inspection equipment is used to examine the hardened liner, ensuring it adheres properly to the inner walls of the pipe.
Additionally, Almco Plumbing conducts hydraulic tests on every project to guarantee that all work meets the established standards.
Materials for CIPP Lining Technology
Materials employed in CIPP lining include polyester, vinyl ester, and epoxy resins. Their main characteristics are as follows:
- Polyester Resins: Economical, offer good strength, and are well-suited for standard conditions.
- Vinyl Ester Resins: Exhibit high chemical resistance, making them ideal for aggressive environments.
- Epoxy Resins: Provide exceptional strength and excellent adhesion to virtually any substrate, rendering them the ideal choice for most projects.
CIPP lining technology stands as the most innovative method for rehabilitating damaged and worn pipelines, combining environmental sustainability, cost efficiency, and a sensitive approach to preserving the urban landscape. Its application across the utilities, industrial, and energy sectors addresses challenges related to minimizing negative impacts on the environment.