Boiler replacement is a critical service for maintaining comfort, efficiency, and safety in commercial buildings. As heating systems age, they often become less reliable, less efficient, and more prone to costly breakdowns—disrupting daily operations. Upgrading to a modern, energy-efficient boiler can reduce operating costs, improve performance, and ensure compliance with evolving safety and environmental standards.
This guide from Almco Plumbing outlines when to consider a boiler replacement, the most common commercial boiler issues in San Diego, and what to expect from a professional installation process.
Contents
What is Boiler Replacement?
Commercial boiler replacement involves removing an outdated, inefficient, or malfunctioning boiler system and installing a modern unit tailored to the building’s specific heating and hot water needs. This process is significantly more complex than residential replacements due to the larger scale and technical demands of commercial systems.
It includes assessing the building’s heating requirements, selecting an appropriate boiler type (such as a combi or industrial model), and ensuring compatibility with the existing infrastructure.
Boiler replacement must also comply with strict local and national safety codes, involve proper sizing to meet efficiency goals, and aim to minimize downtime for the business. When executed correctly, a commercial boiler replacement can greatly improve energy efficiency, lower utility costs, and ensure reliable performance to support daily operations.
Most Common Problem with Boilers in Commercial Property
Boilers in San Diego’s commercial properties face several region-specific issues, especially due to hard water, temperature fluctuations, and high operational demand. Here are the most frequent problems we encounter:
- Inconsistent Heating or Hot Water Supply. This issue often stems from sediment buildup due to hard water, air pockets, or malfunctioning thermostats. Inconsistent temperatures can be disruptive, especially for facilities requiring steady hot water like restaurants or gyms.
- Leaks & Corrosion. San Diego’s hard water accelerates corrosion and mineral scaling. Leaks may occur in valves, joints, or tanks, resulting in water loss, reduced system efficiency, and potential structural damage.
- Pressure Fluctuations. Improper water pressure can lead to serious performance issues. High pressure may cause leaks or damage valves, while low pressure can prevent adequate heat distribution. San Diego businesses must closely monitor pressure due to fluctuations in the water supply.
- Pilot Light or Ignition Failure. Gas-fired systems may suffer ignition problems caused by dirty burners, faulty thermocouples, or malfunctioning gas valves—resulting in system shutdowns during peak usage hours.
- Frequent Cycling (Short Cycling). When a boiler turns on and off too often, it’s often due to a miscalibrated thermostat, incorrect boiler size, or limescale buildup. Inconsistent demand patterns and poor maintenance often make this worse.
- Unusual Noises. Whistling, banging, or gurgling sounds typically point to air trapped in the system, a failing pump, or blockages. These noises are early signs of larger issues and should not be ignored.
- Control System Failures. Modern commercial boilers rely on electronic controls. Failures in sensors or wiring can lead to poor performance, shutdowns, or inefficient energy use—often requiring immediate attention.
- Reduced Efficiency. As scale builds up inside the system due to San Diego’s mineral-rich water, heat transfer becomes less effective. The result: longer heating cycles, higher gas bills, and more wear on the system.
- Environmental Considerations. Older systems may no longer meet California’s strict energy efficiency or emission standards. Replacement is often the only viable way to remain in compliance and avoid penalties.
By addressing these challenges now, San Diego businesses can ensure that their boiler systems are operating efficiently and in compliance with local standards.
Step-by-Step Boiler Replacement Process
Replacing a boiler is a complex job that requires professional expertise to ensure safety, efficiency, and compliance with local codes. Here’s a step-by-step overview of the professional boiler replacement process.
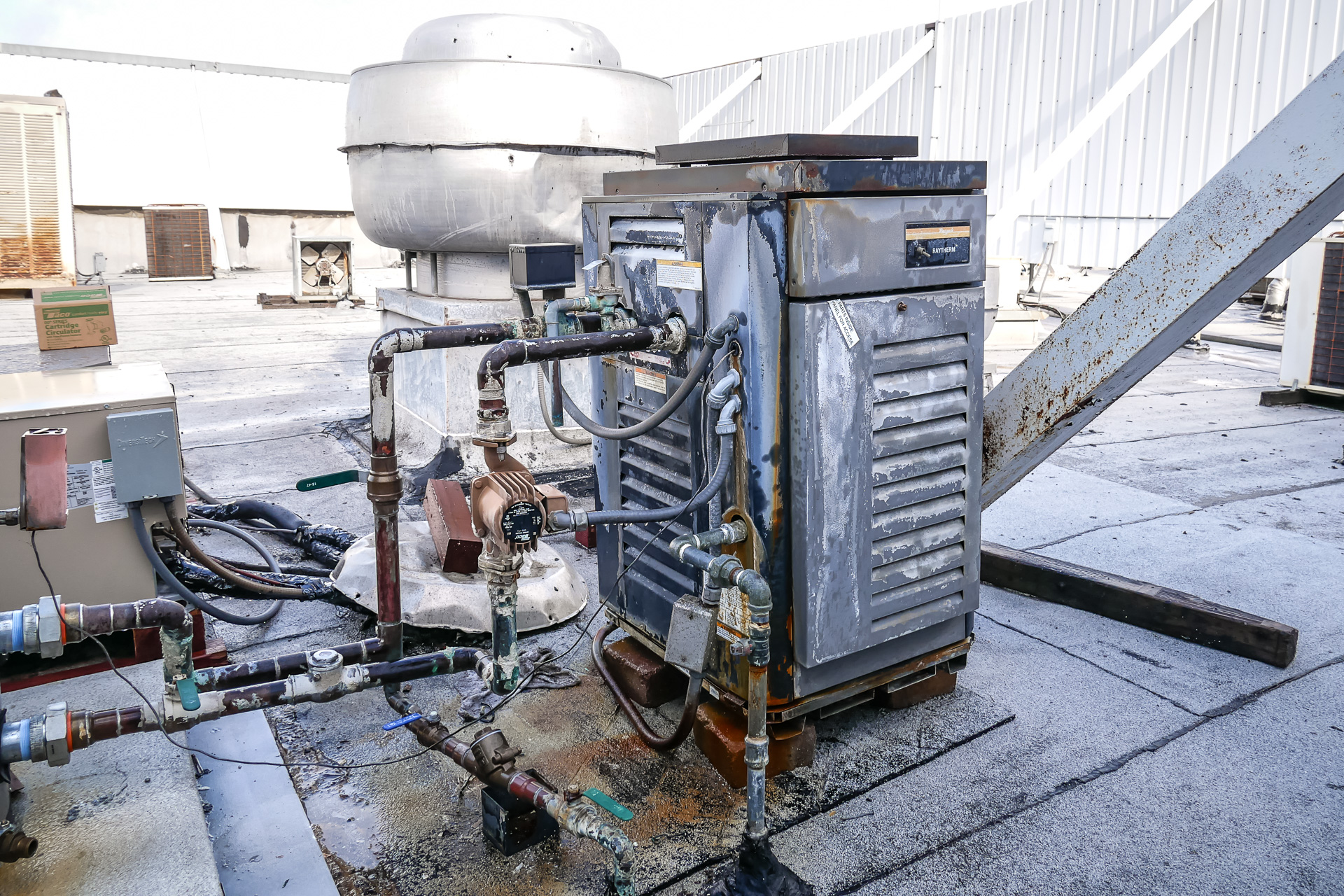
Safe decommissioning: The engineer safely disconnects and removes the old boiler, ensuring proper disposal in accordance with environmental regulations.
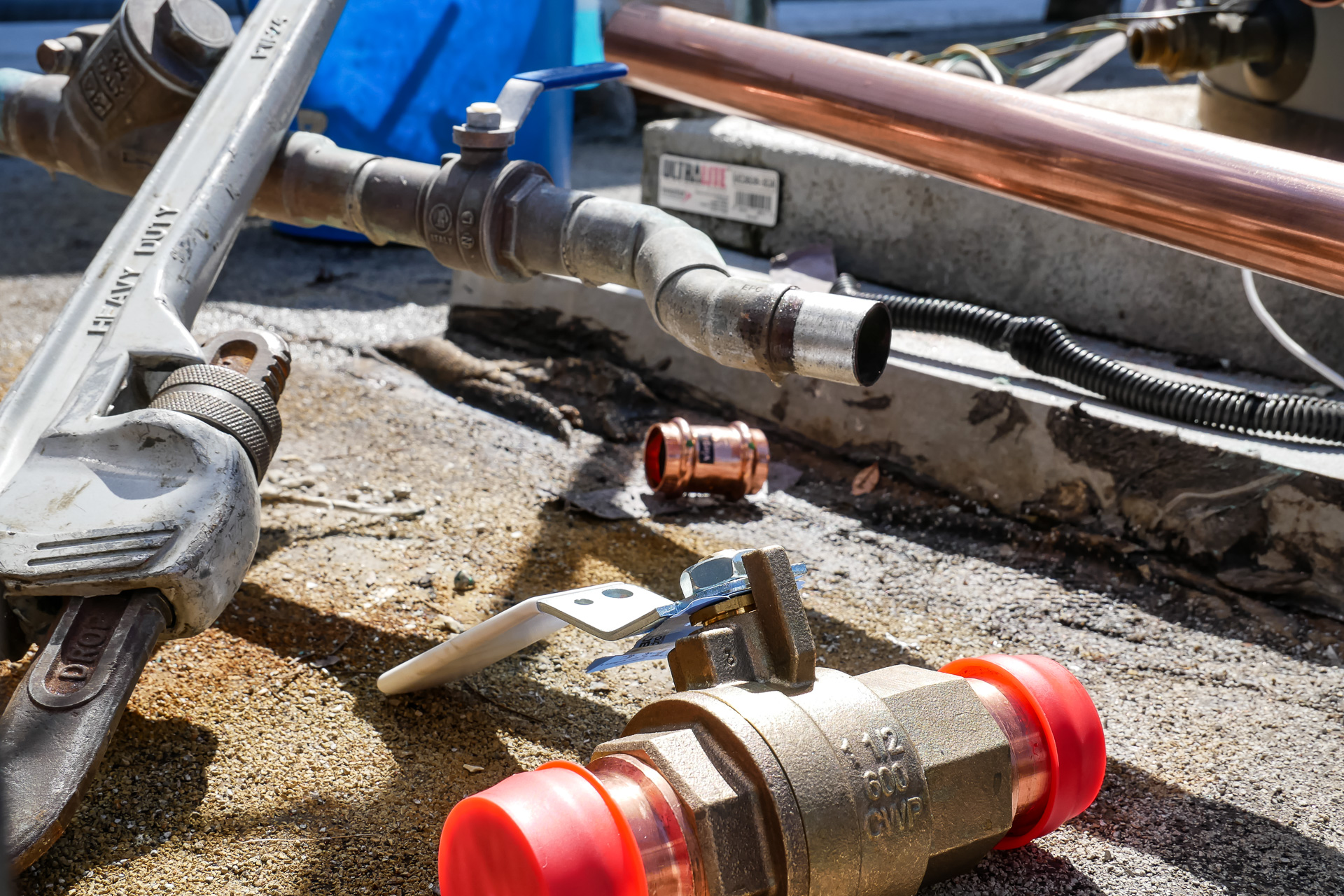
System preparation: The existing heating system is flushed to remove any debris or sludge that could hinder the performance of the new boiler. This may involve a chemical or power flush, depending on the system’s condition.
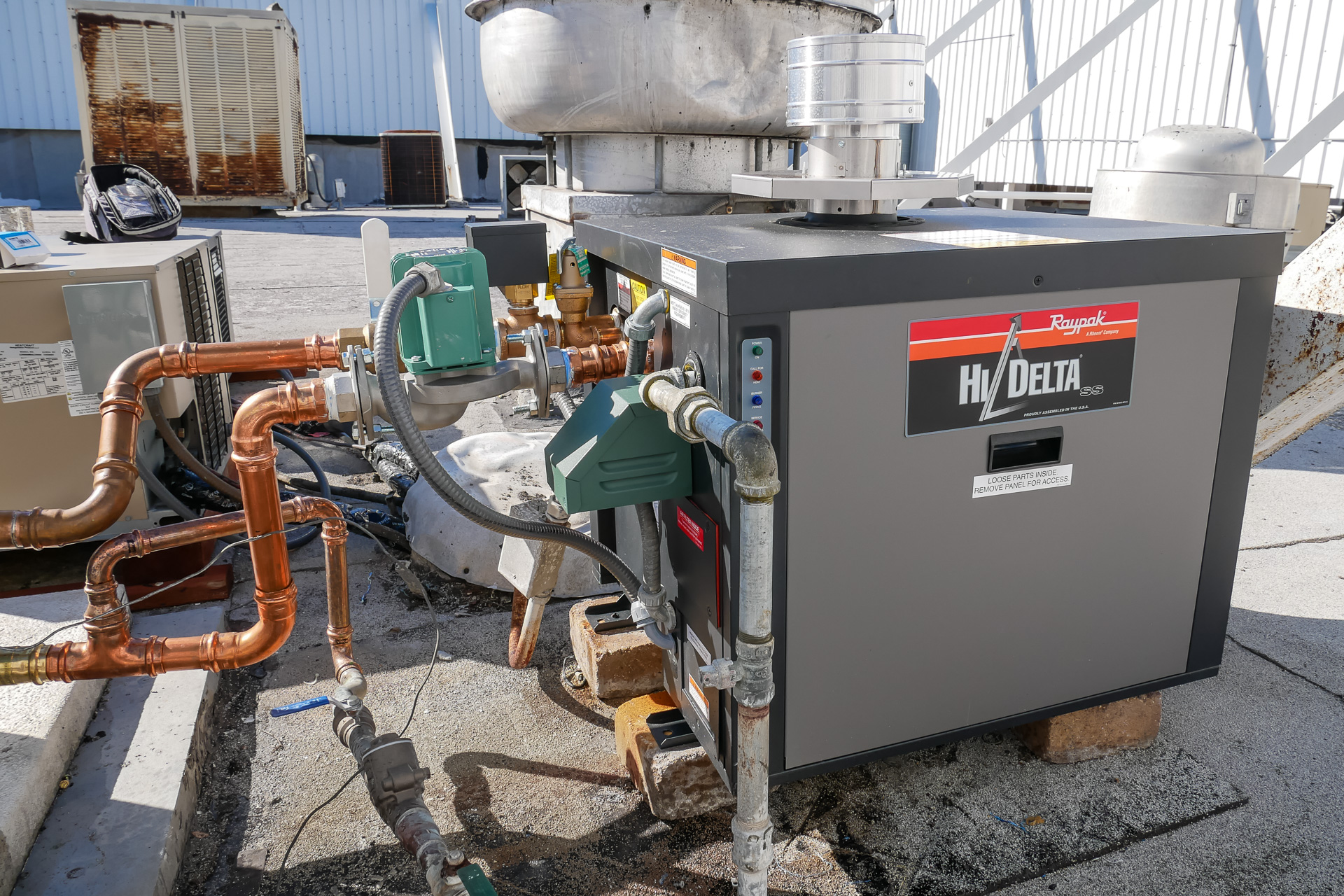
Positioning and connection: The new boiler is installed in the predetermined location, with all necessary connections to water, gas, and electricity completed safely. The flue system is also installed to vent exhaust gases properly.
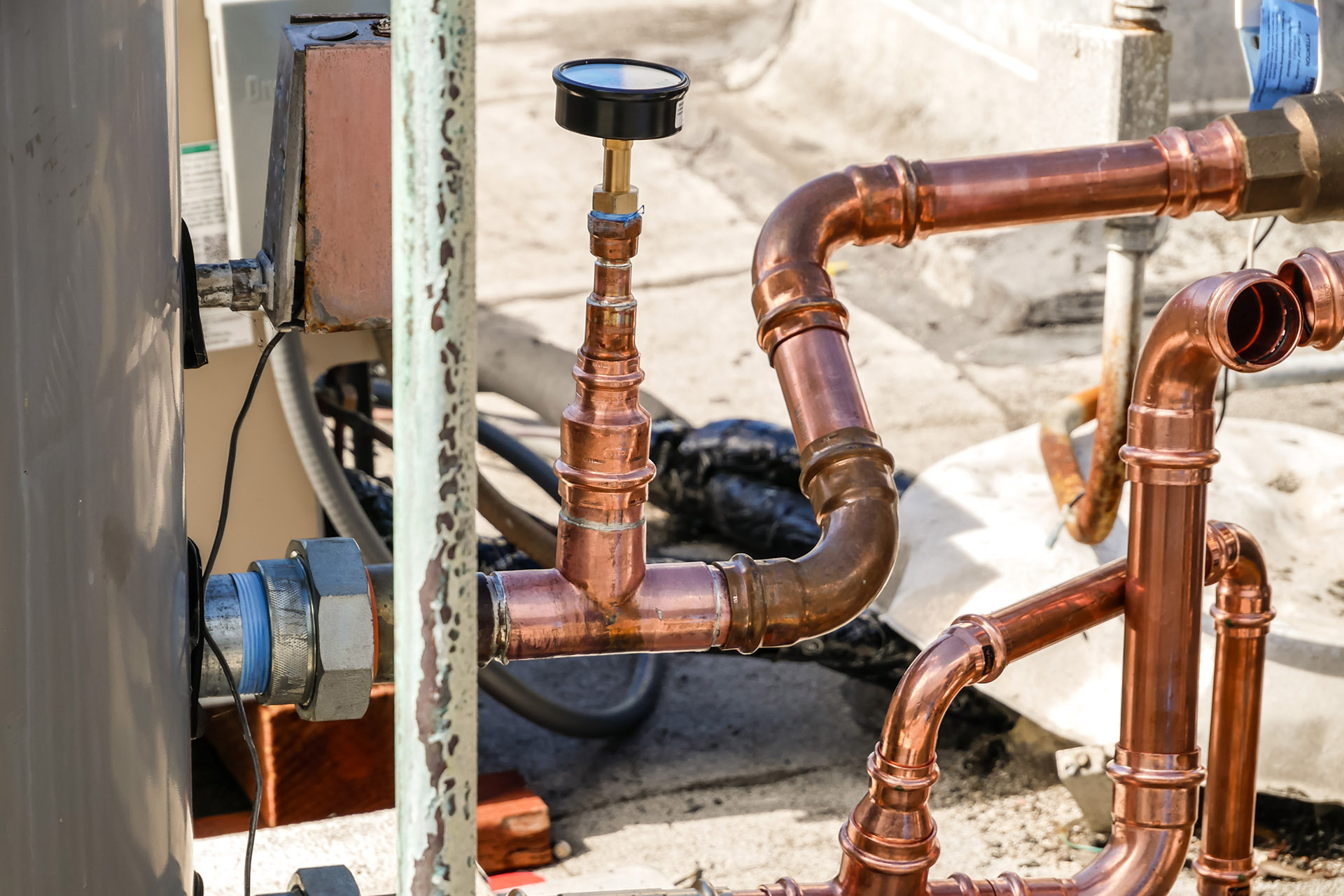
Ensuring proper operation: The engineer conducts a series of tests to verify that the new boiler is functioning correctly and efficiently. This includes checking for leaks, confirming gas pressure, and ensuring proper combustion.
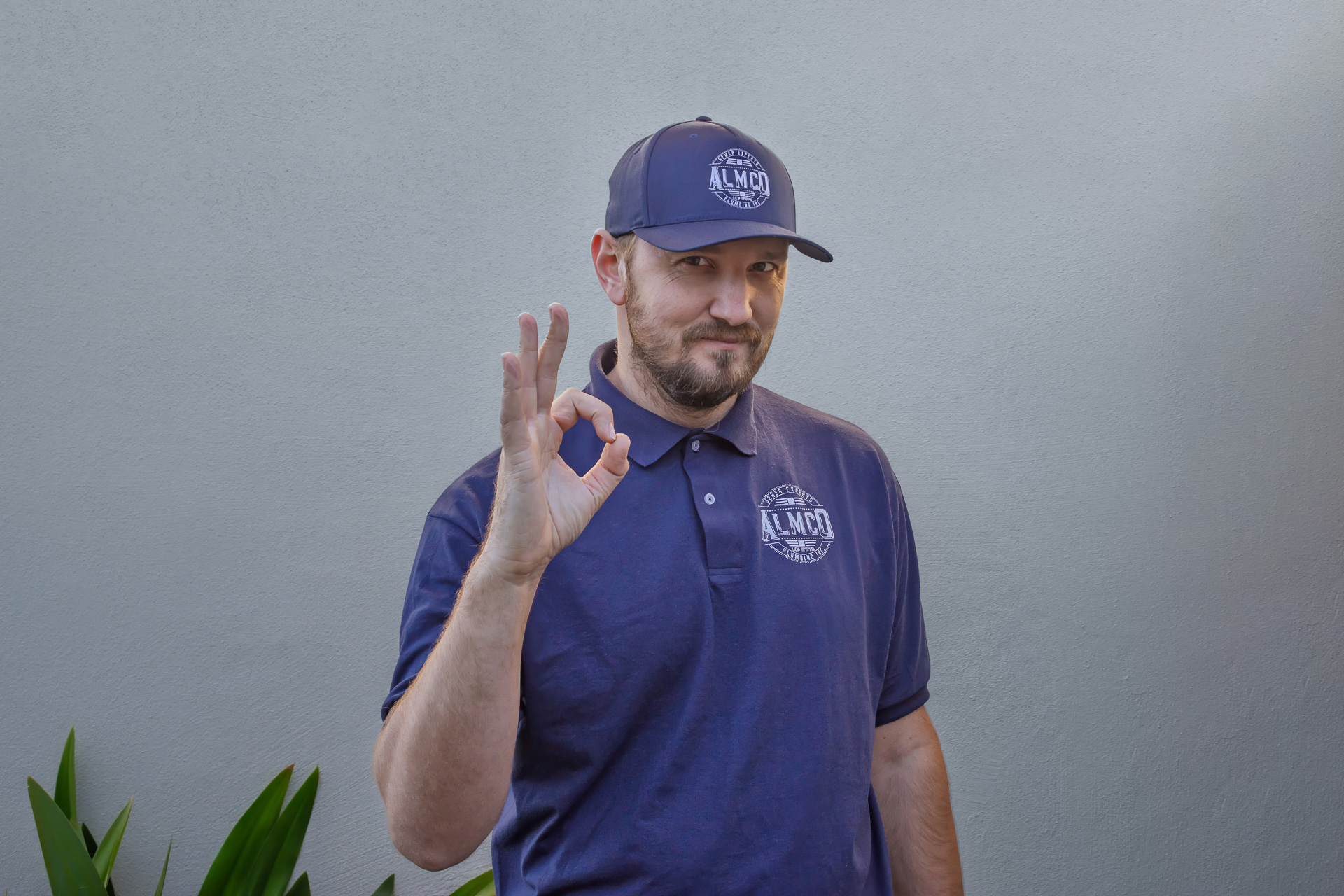
Ongoing maintenance: Professional installers often provide maintenance services to keep your boiler running efficiently. Regular servicing is recommended to extend the lifespan of the unit and maintain its warranty.
By following this comprehensive process, professional heating engineers ensure a smooth and efficient boiler replacement—resulting in a reliable and safe heating system.